Intelligent Machines
Nanotube Motor
Artificial muscles could power tiny actuators and microfluidic mixers
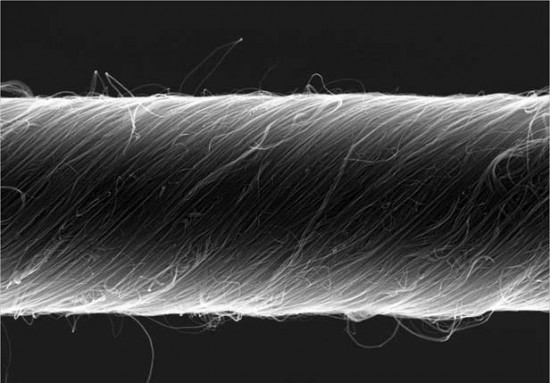
Source: “Torsional Carbon Nanotube Artificial Muscles”
Ray Baughman et al.
Science 334: 494–497
Results: Researchers at the University of Texas at Dallas made nanotube yarn that twists in response to electricity, enabling it to act as a motor. For a given length, it twists 1,000 times more than other materials designed for use as tiny motors, such as shape-memory alloys that change shape in response to heat or another stimulus. The fastest of the nanotube motors spins at 600 revolutions per minute and can generate as much twisting force as a conventional motor. Researchers demonstrated this ability by using it to mix fluids with a paddle.
Why it matters: Making useful motors for very small applications has been difficult because decreasing the size of conventional motors greatly decreases the amount of twisting force they can exert relative to their weight. Even at this scale—just a fraction of a hair’s width—the nanotube yarn can exert as much force relative to its weight as a large motor. It could be useful for moving fluids around in microfluidic devices.
Methods: The researchers used previously developed methods to twist carbon nanotubes together into a thin yarn. They dipped one half of the yarn, along with an electrode, in an electrolyte. They also attached a paddle to the middle of the piece of yarn and anchored both ends to prevent them from rotating. When they applied electricity, ions from the electrolyte were attracted to electrons in the nanotubes. As the ions moved into the yarn, its volume increased, causing it to partially untwist; this, in turn, made the paddle move. When the power was cut, the half of the yarn that wasn’t immersed in the electrolyte acted as a spring that returned the paddle to its original position.
Next Steps: The researchers are now building microfluidic circuits that use the motors as pumps and mixers. They are also starting to make robots the size of bacteria that are propelled by the nanotube yarns.